REFRACTORY MATERIALS
DGC REFRACTORIES: ENGINEERED EXCELLENCE FOR INDUSTRIAL HEAT MANAGEMENT
Welcome to DGC Refractories, a division of DGC South Africa and a proud member of the Dickinson Group of Companies. We’re more than suppliers, we’re strategic partners committed to enhancing thermal performance, reducing operating costs, and increasing reliability across high-temperature industries.
Over a century of service. A future built on engineered resilience.



INTRODUCTION
DGC Refractories offers a comprehensive range of ISO-certified refractory materials developed to meet the evolving needs of industry. Our materials are manufactured in modern production facilities that leverage automated forming, high-efficiency kilns, and advanced process control systems to ensure consistent quality and sustainability.
With over a century of experience in high-temperature industrial services, DGC Refractories combines deep materials expertise with ongoing product innovation and technical support.
QUALITY CONTROL
& QUALITY ASSURANCE
At DGC Refractories, quality is engineered into every step of the process. Our integrated QA/QC protocols ensure every product meets or exceeds the most demanding technical and environmental standards.
WE EMPLOY ADVANCED LABORATORY AND TESTING FACILITIES INCLUDING:
-
ICP-AES Spectrograph – for precise chemical analysis
-
High-Temperature Load Testing – to simulate peak service conditions
-
Image Analysis Microscopy – for microstructural verification
-
Thermal Shock Resistance Testing – for sudden heat cycle performance
-
High-Temperature Microscopy & Dilatometry – for expansion and phase behaviour
WE ALSO PARTNER WITH INDEPENDENT THIRD-PARTY INSPECTION AGENCIES, INCLUDING:
-
China Testing & Certification Group (CTC)
-
China Steel Test Group (CST)
-
SGS and Bureau Veritas (available upon request)

This combination of internal and external quality control ensures every DGC refractory product is reliable, traceable, and ready for critical industrial service.
PRODUCTION CAPACITIES
High-volume. High-assurance. High-performance.
Our scalable manufacturing capabilities ensure responsive delivery for bulk supply or specialised project requirements.
ANNUAL PRODUCTION CAPACITY:
-
Shaped Refractory Bricks – 300,000 tons
-
Graphite Electrodes and Functional Refractories – On-demand by specification
With a global logistics network and warehousing footprint across Africa, we ensure on-time delivery, even in complex, high-volume environments.
PRODUCT RANGE



SHAPED REFRACTORIES
DGC Refractories supplies high-performance shaped products engineered to withstand extreme temperatures, corrosion, erosion, and rapid thermal cycling.
MAGNESIA BRICKS
Outstanding resistance to basic slag and thermal conductivity.
MAGNESIA-CARBON BRICKS
High thermal shock resistance for EAF and ladle lining.
SILICA BRICKS
Excellent refractoriness under load for coke ovens and glass tanks.
MULLITE BRICKS
Durable, thermally stable across varying cycles.
ALUMINA CARBON BRICKS
Suitable for converter and ladle zones.
ANDALUSITE BRICKS
Superior crack resistance under repeated cycling.
SPECIALIZED BRICKS
Si₃N₄-bonded SiC and Sialon-bonded Corundum available on request.






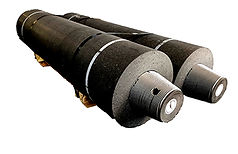
We supply a full range of high-grade graphite electrodes for electric arc furnace (EAF) operations:
-
Regular Power (RP)
-
High Power (HP)
-
Ultra-High Power (UHP)
-
Diameter range: 200mm – 750mm
GRAPHITE ELECTRODES

FUNCTIONAL REFRACTORIES
DGC offers a wide range of functional refractory components used in metallurgical vessel control:
-
Slide Gate Mechanisms
-
Ladle Nozzles
-
Well Blocks
-
Permeable Bricks


These critical components are manufactured to exacting tolerances, ensuring stability, wear resistance, and long life in the most demanding operating zones.
BENEFITS
OF PARTNERING
WITH DGC REFRACTORIES
Innovation. Integrity. Impact.
SUSTAINABLE ENGINEERING
All products are designed with energy efficiency and reduced environmental impact in mind.
EXTENDED SERVICE LIFE
Engineered for resilience and reduced downtime across applications.
COMPREHENSIVE RANGE
From standard linings to specialised custom shapes, we’ve got you covered.
UNCOMPROMISING QUALITY
Backed by rigorous internal controls and third-party verification.





CHALLENGES AND SOLUTIONS
Tailored solutions for complex operating environments.
CUSTOMISED FOR YOUR KILN OR FURNACE
Our technical experts help optimise material selection based on zone, thermal cycle, and chemical exposure.
CONSISTENCY YOU CAN COUNT ON
We deliver high-volume supply and on-time service, even for multi-site operations.
SPECIFICATION-DRIVEN SUPPORT
Whether you’re designing new builds or planning shutdown replacements, we provide data-driven support from concept to delivery.
WHY CHOOSE
DGC REFRACTORIES
DGC Refractories is more than a materials provider. We are your strategic partner in heat management, delivering value through reliable products, expert technical support, and an unwavering commitment to quality.
Our team’s global expertise and local presence ensure the right product, in the right place, at the right time.
We don’t just meet standards, we elevate them.
Partner with us and experience the next level of refractory performance.
INDUSTRY APPLICATIONS






Ready to optimise your refractory supply?