PRECAST REFRACTORY SHAPES FOR COKE OVENS
- DGC AFRICA
- Jun 23, 2022
- 2 min read
Updated: Apr 9, 2024
DGC designs, manufactures and installs a complete range of precast refractory shapes that were specially designed for coke oven wall construction.
The innovative coke oven precast refractory solutions are revolutionary in terms of their manufacturing process, installation speed, lifetime performance as well as environmental and safety performance. The coke oven precast refractory shapes also give manufacturers a competitive advantage as their use results in significant enhancements of ovens’ efficiencies, longevities, and productivity in many ways. This article will further discuss these in more detail.

PROPERTIES OF PRECAST REFRACTORY SHAPES
With dedicated and experienced teams, the company works in collaboration with clients to redesign coke oven walls for the modular blocks to ensure that ovens are repaired in the most cost and time-efficient manner.

By using coke oven precast refractory solutions the following are observed:
IMPROVED LABOUR EFFICIENCY
The complexity of coke oven wall construction is reduced from a highly skilled refractory masonry exercise to a simpler rigging exercise. Manpower requirements may be reduced by up to 80% when compared to traditional methods of construction.
FASTER CONSTRUCTION
Project duration is reduced from the order of several months to mere weeks. This is because the large modular customized blocks with tongue and groove designs help to streamline the process of installation and the highly intuitive repair process. All elements of the walls, including the oven tapers are also built into the modular designs, eliminating guess work from the coke ovens wall construction process.
IMPROVED ENVIRONMENTAL PERFORMANCE & ENERGY EFFICIENCY
Each coke oven precast refractory module replaces about 30 bricks, the solution thus significantly reduces the number of joints within coke oven walls. This decreases leaks, thereby impacting oven efficiencies and lowering emissions.
SAFER MAINTENANCE CAMPAIGNS
DGC’s precast refractory solutions assist in improving the safety profile of coke oven wall demolition and reconstruction. This is because these solutions result in much shorter demolition and rebuild campaigns with much fewer workers onsite thereby drastically reducing human interface and lowering the probability of accidents.
SHORTER HEAT-UPS
Coke oven walls that are based on precast refractory modules only require less than 48 hours of heat up before the flues can be brought back into operation. This is a huge decrease when compared to traditional standard-sized bricks based coke oven walls that could require much longer periods for start-up.


BENEFITS OF PRECAST REFRACTORY SHAPES
Massive cost savings over time.
Streamlined installation processes.
Reduced operating and maintenance costs directly impacting plant profitability.
Maintenance-free modules and reduced post-maintenance costs.
Improved regulatory compliance.


ABOUT OUR COMPANY, HISTORY, AND PARTNERS
Dickinson Group of Companies (DGC) was founded in 1910. For comprehensive information about Our Company – History, Vision & Values, Strategy, Global Alliances, Africa Footprint, Our Commitment to Safety, Anti-Corruption Policy, References, and Industrial Solutions, please visit our website.
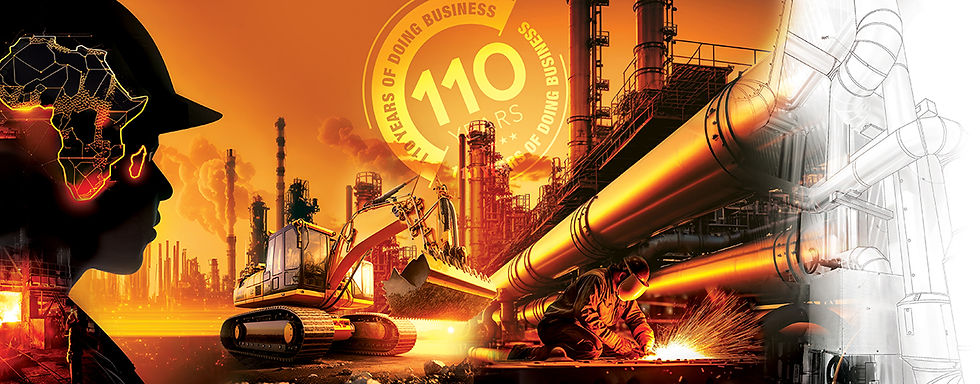
Comments