Justin Nothnagel* discusses how DGC Africa’s inspection services support furnace reliability, safety, and operational efficiency.
In the high-temperature environment of glass manufacturing, the integrity of furnaces is central to operational success. Any compromise in furnace performance can jeopardise product quality, disrupt production continuity, increase safety risks, and elevate operating costs.
Recognising these industry challenges, DGC AFRICA offers non-intrusive furnace inspection technologies designed to support predictive maintenance strategies and enable real-time operational insights.
Where traditional inspection practices depend on scheduled shutdowns and delayed visibility, DGC AFRICA’s proactive approach, featuring high-temperature furnace endoscopy and infrared thermography, provides continuous monitoring of furnace health without interrupting production. This shift from reactive to proactive diagnostics empowers plant operators to address wear, defects, and energy inefficiencies before they escalate into critical issues.
CHALLENGES
Glass manufacturing facilities operate within a high-stakes framework defined by thermal stability, energy optimisation, safety standards, and high-throughput demands. Maintaining reliable furnace performance presents several persistent challenges:
Undetected refractory wear: Internal degradation often advances unnoticed between maintenance cycles.-
Unplanned downtime: Equipment failure can halt production unexpectedly, leading to costly delays and emergency repairs.
Thermal inefficiencies: Compromised refractory linings can lead to significant heat loss and higher fuel consumption.
Safety hazards: Structural failures pose serious risks to plant personnel and equipment.
Limited operational insight: Without ongoing condition monitoring, predictive maintenance strategies are difficult to implement.
These challenges require precise, reliable, and technologically sophisticated solutions that seamlessly integrate with existing operational protocols.
INSPECTION TECHNOLOGIES
DGC AFRICA provides furnace inspection solutions specifically engineered for the demanding thermal and mechanical environments typical of the glass manufacturing industry. By delivering real-time insights through advanced imaging and diagnostics, these solutions enable smarter operational decision-making and long-term asset management.
FURNACE ENDOSCOPY
This inspection method offers internal visualisation of furnace conditions during full operation, allowing operators to detect refractory wear, cracks, and thermal anomalies without halting production. The use of small-diameter probes and high-definition imaging systems ensures non-intrusive access to key internal areas with precise clarity.
Key benefits:
Real-time monitoring during ongoing operations.
Early detection of structural and refractory deterioration.
Improved planning for maintenance and refractory procurement.
Extended furnace lifespan through data-informed interventions.
Reduced reliance on emergency shutdowns and reactive repairs.
INFRARED THERMOGRAPHY
As a complementary technology, infrared thermography enables external thermal analysis of furnace shells. This non-contact method identifies surface temperature anomalies that signal internal refractory wear or heat loss, providing actionable insights without disrupting production.
Key benefits:
Continuous external monitoring of furnace shell temperatures.
Early identification of hot spots and compromised insulation.
Enhanced energy efficiency through optimised thermal performance.
Reduced operational risk via timely detection of overheating.
Predictive maintenance planning based on thermal data trends.
Together, these technologies form a diagnostic framework that supports predictive maintenance, improves plant safety, and enhances overall furnace performance.
BENEFITS
DGC AFRICA’s furnace inspection services go beyond routine diagnostics. They represent a strategic tool for plant operators seeking to improve performance reliability, and cost efficiency.
By embedding predictive diagnostics into the maintenance cycle, clients gain the ability to transition from reactive problem-solving to proactive risk management.
Operational advantages include:
Reduced downtime: Predictive insights enable scheduled maintenance, minimizing unplanned shutdowns.
Lower costs: Early detection reduces emergency repair expenses and improves resource planning.
Increased asset longevity: Timely interventions prevent premature refractory failure.
Improved energy use: Thermal efficiency gains reduce fuel consumption and environmental impact.
Enhanced safety: Real-time monitoring mitigates operational risks and protects personnel.
INDUSTRY PAIN POINTS
The inspection solutions developed and implemented by DGC AFRICA directly address the core challenges faced by furnace-intensive operations. Table 1 outlines how these technologies align with the most pressing concerns in the glass manufacturing sector.

Table 1 : How DGC Africa addresses the core challenges faced by furnace-intensive operations
SUPPORTING GLASS MANUFACTURING
In today’s competitive and resource-conscious industrial landscape, the ability to anticipate failure and mitigate risk is a defining capability. With increasing pressure to reduce downtime, improve safety, and optimise energy consumption, furnace inspections must evolve.
DGC AFRICA collaborates with global technology providers to bring modern inspection tools to the African and international markets, supporting manufacturers in achieving high operational standards while reducing long-term costs.
Through the integration of real-time diagnostics and proactive maintenance planning, glass manufacturers can elevate production reliability, extend asset life, and improve sustainability—all without compromising safety or output.
— * Justin Nothnagel, Director Business Development, DGC Africa, Vereeniging, South Africa

Published in the May 2025 Edition of Glass International
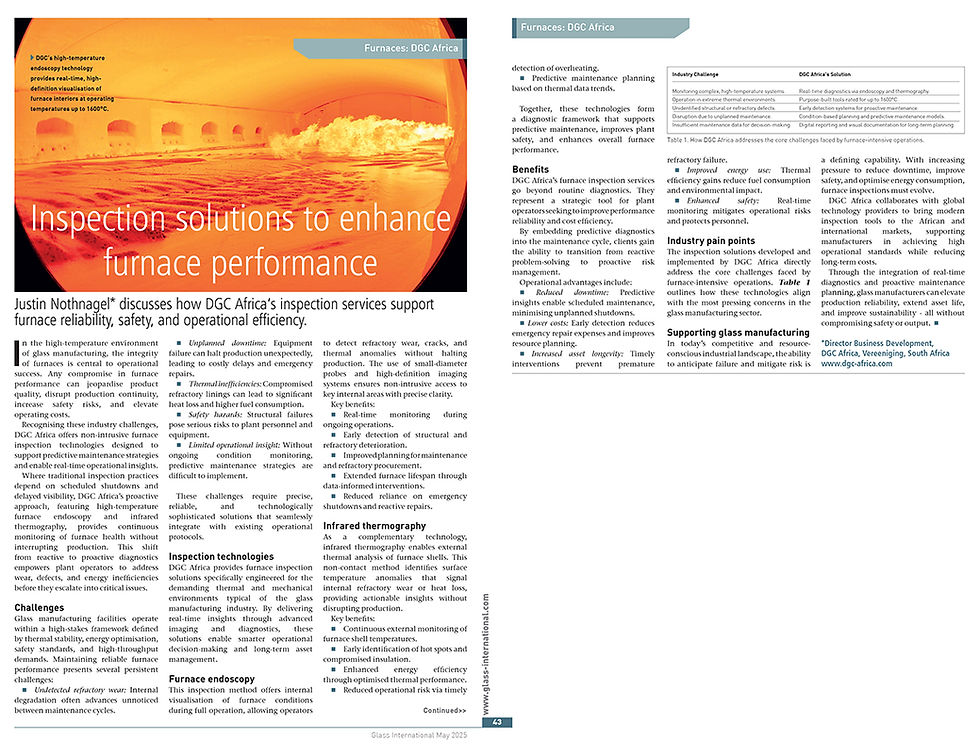